3个质量思维成就企业品控
2018-07-15 11:48 来源:http://www.ceo315.org/ 阅读: 次
著名战略思想家李德・哈特认为,间接路线是最有希望和最经济的战略形式。从质量角度考虑,策略就是要消灭不良品,直接路线是处理它们,而我提出的三个质量思维则属于间接路线。其一,“内建质量”预防不良品的产生;其二,在不良品呈燎原之势前早发现、早解决,把星星之火扑灭;其三,质量管控方法有很多,比如点检表、推移图、柏拉图(帕累托图)、“现地现物”等,最终都要融入到“PDCA循环”中。
内建质量(Built-in Quality)的“三不”政策
Built-in原意是“内置、嵌入”,译成“内建”是觉得对质量体系而言更为贴切。“内建质量”是所有质量思维中最困难的,也是质量挑战的终极目标。举个例子,一个简单的排线连接器,如果装反,得一直到电流测试才能发现。如果把接头形状做成不对称,装反时插不进去,就可以预防错误发生,这种防呆装置如今在组装设计上普遍使用,就属于内建质量保证的范畴。
内建质量是在某一个特定范围里的三不政策:“不接受不良品,不设计或制造不良品,不流出不良品。”特定范围可大可小,小到一个人,大到一个工厂。在流水线生产模式下,要想做到每个工位的内建质量非常困难,所以才在下游布置了许多检测来围堵这些不良品。但从整个工厂来看,如果不良品都能被拦下来,不流到客户端,也算是工厂整体做到了内建质量。
内建质量思维就是激发全员追求完美的工匠精神。唯有所有环节的人(包括企业家、领导)都能找回这种带有某种偏执狂的执着、认真、负责、追求完美的精神,才能把内建质量思维落实到业务当中,将这个思维慢慢地转化为企业的核心价值观。唯有当它体现在产品和服务上、能让客户感受到时,内建质量才能成为竞争对手极难模仿和跨越的核心竞争力。
“早发现、早解决”,难的是“发现”
质量管理的基本思路是上游管控,也就是“早发现、早解决”。但要建立有效的“早发现、早解决”机制不是那么容易。就拿生产来说,来料的抽检不能保证100%上线的料没有不良品;生产线上的工人不可能不出错;机台用久了不会没有瑕疵;测试仪器也会有校准或量测不到位的时候;品检也有眼花误判的概率……凡此种种,都会产生不良品或将不良品放出去。要想杜绝不良品流出,就得从头到尾设置许许多多的风险预警、识别装置或手法来早发现、早解决。
不过,不是所有不良品的产生都容易及早识别的。譬如汽车车身钣金的焊接,一辆汽车全身大概有3000多个焊点,其中十分之一是和安全相关的。如果焊点的强度不够,当碰撞发生时这些焊点会撕裂,可能造成车身重要结构变形或断裂,使乘客受伤。但焊点强度够不够,取决于焊接时的许多参数,焊完后的焊点好坏是很难用肉眼分辨出来的。可又不能把焊点一一撬开检查焊接面,对这个重要隐患的“早发现、早解决”就成了车身焊接厂的难题,到今天都不能找到一个办法保证100%的焊点在强度标准内。
而且,越简单的思维往往越难执行到位。“早发现、早解决”的难点在于发现而不是解决。能够在表面正常的情况下,嗅到危机的风险就能够及早采取防范或应变措施,虽然不见得让危机消弭于无形,但可以大大降低损害的程度。而风险轻重的判断却因人而异,这和能力、经验有关。
从事质量工作的人除了解决问题外,价值还体现在识别质量风险的征兆上。几年前我加入一家公司,分管质量。当时他们正准备在美国市场推出第一款4G智能手机,我在第一次参加项目进展会后,马上警觉到这个项目要出大问题。此时离放量不到三个月,许多设计已经固化,无法修改,但客户要求的上市时间却不容更动。评估了整体质量、交付风险后,我当机立断主导整个项目,重新评估缺失和补救方案,最终使得这款手机准时上市,保护了客户的声誉。后来这款手机在上市后质量深获好评,客户订单也大幅增加。
“早发现、早解决”不仅适用于产品质量,在员工管理上也可借鉴。2010年发生富士康员工“跳楼事件”时,我正任职某事业群华南区负责人。当时我处理了上千件员工“关爱”案子,包括亲手救下两名有极强自杀倾向的员工(根据当时处理的心理医生说,再晚一小时发现,后果不堪设想),用的就是这些年积累下来的“早发现、早解决”质量思维。
爬楼梯上升式的PDCA循环
质量改进永不停止,但追求持续改进不能操之过急,应从小处着手,慢慢扩展。PDCA循环正是推动持续改进的重要方法之一。PDCA代表了持续改进的四个主要步骤:
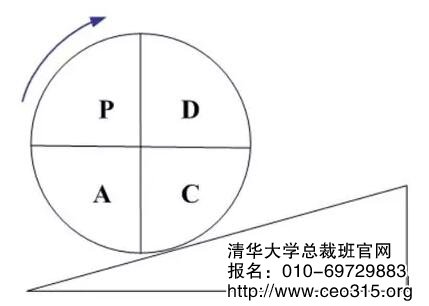
1、P(Plan,计划):仔细分析现状,和目标对比,看看缺口在哪里,然后详细规划改善的步骤。
计划可以分几个步骤:一是先把问题和目标定义清楚;二是利用各种工具,譬如作业流程图、鱼骨图等,把和问题相关的流程和因素梳理出来,定个优先顺序;三是进一步拆解流程,把各步骤仔细分析,看看毛病可能出在哪里。
2、D(Do,执行):根据计划,动手改进。
事先得想好退出计划,以防万一改善失败。动手时应从小处切入,谨防破坏现有流程,造成系统瘫痪。如果解决方案不止一个,应该设计一个实验,评估可能方案的优劣。
3、C(Check,检查):监控改进过程。
确认量测工具和方法维持不变,否则可能误判。结果数据出来后,仔细分析,看看哪种方案比较有效,而且对原来流程的变更幅度最小。
4、A(Act,改进):确认改善的确有效,不良和缺陷已经消除后,导入及固化流程,改写规范。
若改善无效,则检讨原因,修改计划,重新启动另一轮PDCA。
PDCA循环是爬楼梯上升式的循环,每转动一周,质量就提高一步。一轮循环结束了,也许只解决了问题的一部分,或者在解决的过程中又衍生出新的问题,因此必须再进行下一轮PDCA循环。如此循环不已。
“不因‘善’小而不为”是持续改进的基本精神。当然这里的“善”是改善的意思,不是善恶的“善”。千万不要忽视小的改善,往往一点点改进就能让客户笑口常开。从“小善”开始也是提醒大家不要忽视改善可能带来的阻力。并不是每个人都会拥抱改善。事实上,大部分人都会抗拒改变,这是人性,因为他们还没看到改善的成果,却要面对改善行动带来的不便。
此外,值得一提的是和PDCA相辅相成的企业习惯——复盘。复盘可以看成PDCA环和环之间的连接,有了它,PDCA才能环环相扣、周而复始。坦率地说,我所经历过的大大小小复盘基本都是做样子。成效比较大的也都偏向于技术层面,而流程、系统、管理上的复盘,因为牵扯到人,比较敏感,因此成效有限。我认为有两个原因。
第一,国人没这习惯。人们内心是否有反省我无法得知,不过公开的真不多见。这恐怕和我们的文化有关。中国有句老话:得饶人处且饶人。当我们把反省与责人(或自责)画上等号时,这个反省会议就变成谁也不想触碰的烫手山芋了,因为我们好面子,既不想公开“羞辱”别人,更不愿自辱。就算勉强做了,也是虚应故事一番,所以复盘的效果始终有限。
第二,与企业文化有关。企业文化是讲究配套的,单一的文化如果没有适当的支撑,在企业里是不可能存活的。譬如企业一方面鼓励流水线的工人遇到质量问题可以停线,但每次一停线班组长就责怪工人,抱怨他每停一分钟浪费了多少产能,公司损失了多少营收。这种重视质量的呼吁和实际行为的不匹配是培养不出任何文化或价值观的。当复盘是一个习惯时,也就变成企业文化的一部分。如果养不成复盘的习惯,就得检视企业文化的方方面面有没有一致,有没有特例,员工愿不愿意接受。最重要的是中级主管能不能承上启下,不断推动它。
从企业整体运营来说,质量是不能独立于其他功能之外的。以生产制造为例,要想持续生产出有效率、质量好的产品,必须在所有的功能(计划、来料、工程、人力、设备、物流、质量等)之间形成一个可协作的节拍。质量思维是公司文化的一部分,附着在每一件事情上面。有了正确的质量思维,方能认知到质量不只是一份工作,而是一种信念,也是企业的良心。
阅读过本文的访客还阅读过: 企业领导要凭借过硬的质量降低成本
庄子:不一样的思维方式,不一样的人生
高潜人才素质深度观察:无边界思维
你是否具有管理者思维?
企业组织结构的四种新形态
所有企业经营者必须回答的3个命题
集合智慧时代,领导者的3个全新角色
陈春花:不是增长型思维?你已经开始自我淘
陈春花:增长型组织该具有怎样的思维模式?
在知识社会里更好的生存,你必须掌握这3个
相关热词搜索:
3个质量思维成就企业品控 相关课程
清友会人力资源总监(CHO)创新实战高级研修班
清大厚德工商管理与创新经营总裁研修班
清友会金融后E董事长研修班
新华商EMBA总裁高级研修班
大健康产业总裁高级研修班
电子商务与互联网思维管理高级研修班